Repairing a modern type of cartridge faucet can be one
of the easiest home repairs that you can do. In
general, anybody can do this, with or without
experience with plumbing. In fact, you can even coach
someone over the phone about the whole process and
still get good results. All you would need is pay
close attention, and you would be done in no time!
General Problems
The most common problems encountered in cartridge
faucets, is usually caused by a problem in the
interior cartridge, which usually wears and tears over
time. Nevertheless, there is no need to worry since
this type of faucet was created with simplicity of
repair in mind.
Getting Started: Purging The Lines
To start off, you need to purge your water lines. In
order to do this, you should turn off the entire water
source that is running to your faucet. Try looking
beneath your faucet and there you can see the shut off
valve that cuts of the water source. If you don’t have
one somewhere near your faucet, then you would have to
turnoff the main valve.
If you have to deal with the main valve, take note
that it would take you longer to purge. Most
households have a shutoff valve feature that is
directly placed under the sink, so it is the least of
possibilities that you need to shutoff the main valve.
After you have cut the water source, turn on the
faucet. Let the water keep on running. Try to wait
until all the water in the pipes has emptied, and
before you proceed to the next step, double check
first if the water lines are really empty.
Working On The Faucet
Now, to start working on the faucet itself, you need
to remove the sink handles. You would have to unscrew
them. Locate the protective cap and pop it off. This
is where you would usually find the screw. You can use
a butter knife or a screwdriver to do the trick. While
doing this, try to be very careful so that you do not
scratch it. In this way, it would still look nice
after the job. Now you can start unscrewing the knobs
until you completely remove them.
If you already know which type of cartridge it is that
you need, then the better. If you don’t you can simply
bring your old one to your local hardware and people
there will be able to help you out.
Once you get the new cartridge, go back and install
it. Then, replace the knobs. Turn the water back on.
When you are done with this, try testing out the water.
If the test runs smoothly without problems, then
you are done.
However, if you experience some water leaks during the
test, you have to do some adjustment again. Turn off
the water source and take off the knobs once more. Try
to check and ensure that you placed the cartridge in
the right position. If it’s not, then try to maneuver
it into the right place.
Put the knobs back into place and turn on the water
source again. Try the water test once more. If this
time it runs smoothly, then you have reached success
with your repair. If you are still experiencing
problems, then you may have a problem coming from a
different source.
Dan and Deanna "Marketing Unscrambled"
Marketing Unscrambled,Home edition is tips to help with interior decorating,curb appeal,tips to help with remodeling,updating the home,buying and selling of real estate tips,
Saturday, May 29, 2010
Saturday, May 22, 2010
Cracks In A Basement Wall - How To Evaluate It?
If you are seeing some cracks on your walls, there is
no need to panic. This can have no significance at
all. However, there are some that can signify that you
are experiencing a big structural defect. If this is
the case, then you would have to do the appropriate
action for the case. This is why proper evaluation
should be done.

Noticing The Problem
Most often, cracked foundation walls are given
attention when a property is being sold in the market.
Even though the owner would insist that the cracked
wall has been like that "forever", the buyer has a
tendency to become concerned about the situation.
Whether you are a buyer, seller, or some one who is
simply concerned about their wall, here are some
important points on evaluating your wall if it needs
repair or not.
Causes And Factors Of Wall Cracking
Foundation walls that are built using concrete blocks
are much predisposed to having cracks than solid
concrete walls. This is especially true if an 8-inch
block was used for the block wall.
Of course, foundation walls should support a
building’s the vertical weight. Plus, if its around a
full basement, it should be able to resist lateral or
inward pressure from the soil outside that are against
the wall. If water saturates the back fill or soil,
then the inward pressure could easily overload your
block wall, which can result into cracks.
Additionally, roots of large and moderate sized trees
that are near your foundation wall can also cause you
major wall problems. Most of the time, roots grow
toward your walls due to the water accumulation along
it.
Seeing The Signs
Horizontal cracks on mortar joints are usually caused
by too much inward pressure against its block
foundation. If you see a horizontal crack that is
about high as half of the wall, then this can be one
sign of too much lateral pressure from the soil.
Sometimes, you may also find some step cracks or short
and small horizontal and vertical cracks near the end
of a wall. This too is a variation of soil pressure
cracks.
When To Be Alarmed
Usually, block foundation walls can remain cracked for
about a number of years without any noticeable
cracking additions or inward bulging. But, the moment
you get a horizontal crack, your wall’s structural
integrity is very much reduced. Additionally, if the
soil back fill is saturated, especially during rainy
days, the number of cracks could increase or, worse
comes to worst; your wall foundation can collapse.
Solution Choices
Problems like these are possible to be permanently
repaired. In fact, there are methods in which you do
not need to have a complete replacement, provided that
the inward movement doesn’t exceed one inch in
relation to the bottom of the wall. You can usually
find the maximum inward deflection where the
horizontal crack is and near its mid-height.
One method you can do is bracing your wall with
reinforced block piers or steel post-braces. However,
if you are concerned with the cost, you may want to go
for steel post-braces since they are less expensive
than the other. However, if it is the overall look you
are after, then you may want to use piers since they
can give a better finished appearance.
It might be needed to call in an expert in this field
but this gives you what you need to know to evaluate
the condition to know when the expert if needed.
Dan and Deanna "Marketing Unscrambled"
no need to panic. This can have no significance at
all. However, there are some that can signify that you
are experiencing a big structural defect. If this is
the case, then you would have to do the appropriate
action for the case. This is why proper evaluation
should be done.

Noticing The Problem
Most often, cracked foundation walls are given
attention when a property is being sold in the market.
Even though the owner would insist that the cracked
wall has been like that "forever", the buyer has a
tendency to become concerned about the situation.
Whether you are a buyer, seller, or some one who is
simply concerned about their wall, here are some
important points on evaluating your wall if it needs
repair or not.
Causes And Factors Of Wall Cracking
Foundation walls that are built using concrete blocks
are much predisposed to having cracks than solid
concrete walls. This is especially true if an 8-inch
block was used for the block wall.
Of course, foundation walls should support a
building’s the vertical weight. Plus, if its around a
full basement, it should be able to resist lateral or
inward pressure from the soil outside that are against
the wall. If water saturates the back fill or soil,
then the inward pressure could easily overload your
block wall, which can result into cracks.
Additionally, roots of large and moderate sized trees
that are near your foundation wall can also cause you
major wall problems. Most of the time, roots grow
toward your walls due to the water accumulation along
it.
Seeing The Signs
Horizontal cracks on mortar joints are usually caused
by too much inward pressure against its block
foundation. If you see a horizontal crack that is
about high as half of the wall, then this can be one
sign of too much lateral pressure from the soil.
Sometimes, you may also find some step cracks or short
and small horizontal and vertical cracks near the end
of a wall. This too is a variation of soil pressure
cracks.
When To Be Alarmed
Usually, block foundation walls can remain cracked for
about a number of years without any noticeable
cracking additions or inward bulging. But, the moment
you get a horizontal crack, your wall’s structural
integrity is very much reduced. Additionally, if the
soil back fill is saturated, especially during rainy
days, the number of cracks could increase or, worse
comes to worst; your wall foundation can collapse.
Solution Choices
Problems like these are possible to be permanently
repaired. In fact, there are methods in which you do
not need to have a complete replacement, provided that
the inward movement doesn’t exceed one inch in
relation to the bottom of the wall. You can usually
find the maximum inward deflection where the
horizontal crack is and near its mid-height.
One method you can do is bracing your wall with
reinforced block piers or steel post-braces. However,
if you are concerned with the cost, you may want to go
for steel post-braces since they are less expensive
than the other. However, if it is the overall look you
are after, then you may want to use piers since they
can give a better finished appearance.
It might be needed to call in an expert in this field
but this gives you what you need to know to evaluate
the condition to know when the expert if needed.
Dan and Deanna "Marketing Unscrambled"
Thursday, May 20, 2010
Do It Yourself - Fixing The Squeaking Doors In The Home!
Squeaking doors can be a really irritating problem.
Although many would consider it to be a major problem,
it isn’t! In fact, it’s a minor house problem that
even you yourself can fix, and here’s how to.

Stop, Look And Listen
First, you should know where that squeaking sound is
coming from. You can do this by stopping, looking and
listening carefully. You should perform the "swing
test" first before you go off buying a whole new door.
Start off by making sure that your surroundings is
quiet. Then, you should stand on the side of the door
in which you remember that the squeak was loudest.
When you’re in position already, swing the door in a
gentle manner, covering its complete arc. Do this
action repeatedly and try to vary the speed while
doing so.
While swinging the door, you should take note of some
factors. Try to note exactly where the squeak comes
from. Then try to note when it is loudest. See whether
it is loudest when you swing the door fast or slow.
Then lastly, find out why exactly the squeak is
happening. Finding out why is a very crucial factor,
since this dictates what remedy you should use.
Two General Remedies
Once you’ve determined where the squeaks are, you can
do two general remedies. First, tighten all the screws
in the hinges. Then, get a flat-headed screwdriver.
Carefully tap its blade in between the hinge body and
the hinge-pin head to separate them.
After doing this, get a 3-in-1 sewing machine oil and
squeeze in a few drops of it into the small space
between the pin-head and the hinge body. If you don’t
have sewing-machine oil, you can also use a WD-40, and
spray some into the same space.
By applying some lubricant in the space, you enable
the lubricant to seep in into the remaining length of
the pin, which is inside the hinge body. Thus, you
give the best lubrication coverage that you can give
for the hinge.
Doing this would generally resolve your squeaking
problems-if you were accurate on determining the
source, that is. However, if you pinpointed the wrong
source, then most probably your squeak would still be
there.
All Hope Is Not Lost
If you pinpointed the wrong source of the squeak,
don’t worry then! By this point in time, you have
determined that the hinges are not the problem. Then,
most probably it’s a wood on wood kind of squeak
problem.
To solve this kind of squeak, you would have to do the
squeak test again. After which, you have to release
the bind, since the problem may be the hinge binding
on the wood. While performing the swing test, heed on
how the door’s hinge-side settles into the door-jamb.
Also, take note of how it makes a final contact with
your door-stop.
This is when stop, look and listen wouldn’t be enough,
since you would have to make use of touch. If you feel
that it has springy feel, when the door is
approximately in the closed position, odds are very
good that it is hinge-bound. This can be the cause of
the squeak since the door is forced to rub with the
jamb material. To repair this kind of problem, you
need to remove your door by removing the screws on the
hinges’ jamb side and leaving the hinges intact with
the door itself. Then, you need to chisel out some
hinge recesses towards the direction of the hinge
barrel. Then, reinstall the door and perform the swing
test again.
If this doesn’t solve your problem, try chiseling out
more recess. It can be a trial and error process.
However, it can be fixed.
Dan and Deanna "Marketing Unscrambled"
Although many would consider it to be a major problem,
it isn’t! In fact, it’s a minor house problem that
even you yourself can fix, and here’s how to.

Stop, Look And Listen
First, you should know where that squeaking sound is
coming from. You can do this by stopping, looking and
listening carefully. You should perform the "swing
test" first before you go off buying a whole new door.
Start off by making sure that your surroundings is
quiet. Then, you should stand on the side of the door
in which you remember that the squeak was loudest.
When you’re in position already, swing the door in a
gentle manner, covering its complete arc. Do this
action repeatedly and try to vary the speed while
doing so.
While swinging the door, you should take note of some
factors. Try to note exactly where the squeak comes
from. Then try to note when it is loudest. See whether
it is loudest when you swing the door fast or slow.
Then lastly, find out why exactly the squeak is
happening. Finding out why is a very crucial factor,
since this dictates what remedy you should use.
Two General Remedies
Once you’ve determined where the squeaks are, you can
do two general remedies. First, tighten all the screws
in the hinges. Then, get a flat-headed screwdriver.
Carefully tap its blade in between the hinge body and
the hinge-pin head to separate them.
After doing this, get a 3-in-1 sewing machine oil and
squeeze in a few drops of it into the small space
between the pin-head and the hinge body. If you don’t
have sewing-machine oil, you can also use a WD-40, and
spray some into the same space.
By applying some lubricant in the space, you enable
the lubricant to seep in into the remaining length of
the pin, which is inside the hinge body. Thus, you
give the best lubrication coverage that you can give
for the hinge.
Doing this would generally resolve your squeaking
problems-if you were accurate on determining the
source, that is. However, if you pinpointed the wrong
source, then most probably your squeak would still be
there.
All Hope Is Not Lost
If you pinpointed the wrong source of the squeak,
don’t worry then! By this point in time, you have
determined that the hinges are not the problem. Then,
most probably it’s a wood on wood kind of squeak
problem.
To solve this kind of squeak, you would have to do the
squeak test again. After which, you have to release
the bind, since the problem may be the hinge binding
on the wood. While performing the swing test, heed on
how the door’s hinge-side settles into the door-jamb.
Also, take note of how it makes a final contact with
your door-stop.
This is when stop, look and listen wouldn’t be enough,
since you would have to make use of touch. If you feel
that it has springy feel, when the door is
approximately in the closed position, odds are very
good that it is hinge-bound. This can be the cause of
the squeak since the door is forced to rub with the
jamb material. To repair this kind of problem, you
need to remove your door by removing the screws on the
hinges’ jamb side and leaving the hinges intact with
the door itself. Then, you need to chisel out some
hinge recesses towards the direction of the hinge
barrel. Then, reinstall the door and perform the swing
test again.
If this doesn’t solve your problem, try chiseling out
more recess. It can be a trial and error process.
However, it can be fixed.
Dan and Deanna "Marketing Unscrambled"
Saturday, May 15, 2010
Tips On Tiling A Floor !
Tiling is one job that most people would rather not
learn how to do since it can be scary that you make
some mistakes in the process. However, it is actually
a lot easier than what many might think. In fact, it
can save you a whole lot of money contrast to hiring a
professional for the job. As long as you know the do’s
and don’ts, then this task is a no-brainer for you.

Choosing Your Tiles
To start off, you have to choose the tiles that you
want to use. You may get surprised with the number of
variety choices when doing this. Tiles may come in
different sizes, colors, textures, materials and
finishes. There are times that you may encounter tiles
with odd sizes. This is done on purpose by companies
so that you would have to buy extra.
Choosing a tile highly depends on you. It can also
depend on how you want the room to be and the over all
design and feel of the room.

Measurements And Computations
You also need to measure out your floor area. You also
have to deliberate on whether you want the tiles to go
under any kind of fittings and units. Generally, it is
better if you tile under the fittings. This is because
if you would have to move appliances in the future,
like a fridge, then you do not have to lift it up over
the edge of your new tiles.
When you have chosen what kind of tile you want to
use, you need to do some computations. You have to get
your floor’s width and divide it by the width of one
tile. This is to know the number of complete rows that
you’ll have. Also, this can help you decide the
optimal wall edge to place your cut tiles against.
It is better to plan it out and measure twice and cut
once than to have to use up a lot of tile by having the
wrong cuts.

Application
Make sure that the sub - floor is level. If it is not level
it will cause the tile to crack and break. If it is not ask
when you are buying the tile what you need to do to fix
it before you start laying the tile. If you do it right the
first time then you will not have to do it again for a long time.
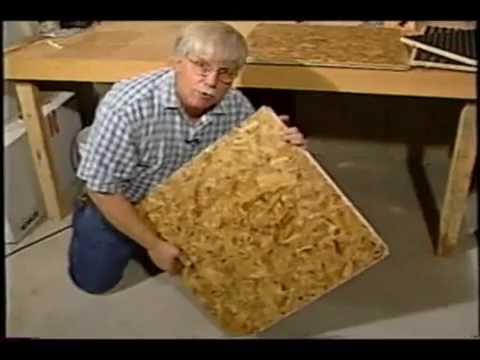
After doing the math, you can now start applying tiles
on your floor. Be sure that you have an even coverage
of adhesive placed on your sub-floor. The type of
adhesive to use would depend on your sub-floor or the
surface you are tiling. If it is a concrete floor,
then you can use a rapid setting adhesive. However, be
sure that you do not spread too much of the mixture at
once, since it can set as fast as 30 minutes.
If it is a wooden sub-floor, then you need a flexible
adhesive. You can know if an adhesive if flexible if
it is written on the bag or the tub. If you have
slate, then you need to use gray adhesive. If you’ll
be having marble, then you need a white adhesive. This
is so that no color coming from the underside would
bleed and ruin your design.
Where you buy the tile can help you to answer some of
these thing when you buy the tile to make sure you get
the right things for the products that you are using.

Grouting
When you are done fixing your tiles on the floor, and
after you have allowed enough time for it to dry, then
you would have to do some grouting. If you have
natural tiles, like marble, slate, limestone, granite,
travertine, and porcelain, you need to seal them first
before you can grout them. You have to use a
specialized impregnating sealer so that they will be
waterproof and can be more resistant to dirt and
staining.
Mix up the grout and apply it using a grout float to
your tiles. Try to work over the gaps until they’re
all filled. If you have white marble tiles, then you
need to use a white grout instead of gray since the
gray kind can stain the marble.
To finish off, wipe out the excess grouts that are
bulging from your tiles using a sponge. Also, use a
grout finisher or your finger to smooth out the grout
lines. After this, stand back, relax and chill while
you wait for your work to dry up!
Dan and Deanna "Marketing Unscrambled"
learn how to do since it can be scary that you make
some mistakes in the process. However, it is actually
a lot easier than what many might think. In fact, it
can save you a whole lot of money contrast to hiring a
professional for the job. As long as you know the do’s
and don’ts, then this task is a no-brainer for you.

Choosing Your Tiles
To start off, you have to choose the tiles that you
want to use. You may get surprised with the number of
variety choices when doing this. Tiles may come in
different sizes, colors, textures, materials and
finishes. There are times that you may encounter tiles
with odd sizes. This is done on purpose by companies
so that you would have to buy extra.
Choosing a tile highly depends on you. It can also
depend on how you want the room to be and the over all
design and feel of the room.

Measurements And Computations
You also need to measure out your floor area. You also
have to deliberate on whether you want the tiles to go
under any kind of fittings and units. Generally, it is
better if you tile under the fittings. This is because
if you would have to move appliances in the future,
like a fridge, then you do not have to lift it up over
the edge of your new tiles.
When you have chosen what kind of tile you want to
use, you need to do some computations. You have to get
your floor’s width and divide it by the width of one
tile. This is to know the number of complete rows that
you’ll have. Also, this can help you decide the
optimal wall edge to place your cut tiles against.
It is better to plan it out and measure twice and cut
once than to have to use up a lot of tile by having the
wrong cuts.

Application
Make sure that the sub - floor is level. If it is not level
it will cause the tile to crack and break. If it is not ask
when you are buying the tile what you need to do to fix
it before you start laying the tile. If you do it right the
first time then you will not have to do it again for a long time.
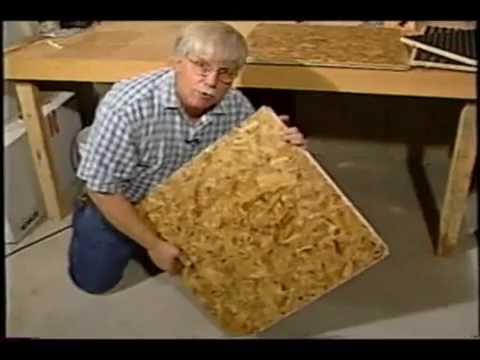
After doing the math, you can now start applying tiles
on your floor. Be sure that you have an even coverage
of adhesive placed on your sub-floor. The type of
adhesive to use would depend on your sub-floor or the
surface you are tiling. If it is a concrete floor,
then you can use a rapid setting adhesive. However, be
sure that you do not spread too much of the mixture at
once, since it can set as fast as 30 minutes.
If it is a wooden sub-floor, then you need a flexible
adhesive. You can know if an adhesive if flexible if
it is written on the bag or the tub. If you have
slate, then you need to use gray adhesive. If you’ll
be having marble, then you need a white adhesive. This
is so that no color coming from the underside would
bleed and ruin your design.
Where you buy the tile can help you to answer some of
these thing when you buy the tile to make sure you get
the right things for the products that you are using.

Grouting
When you are done fixing your tiles on the floor, and
after you have allowed enough time for it to dry, then
you would have to do some grouting. If you have
natural tiles, like marble, slate, limestone, granite,
travertine, and porcelain, you need to seal them first
before you can grout them. You have to use a
specialized impregnating sealer so that they will be
waterproof and can be more resistant to dirt and
staining.
Mix up the grout and apply it using a grout float to
your tiles. Try to work over the gaps until they’re
all filled. If you have white marble tiles, then you
need to use a white grout instead of gray since the
gray kind can stain the marble.
To finish off, wipe out the excess grouts that are
bulging from your tiles using a sponge. Also, use a
grout finisher or your finger to smooth out the grout
lines. After this, stand back, relax and chill while
you wait for your work to dry up!
Dan and Deanna "Marketing Unscrambled"
Subscribe to:
Posts (Atom)